A Comprehensive Guide to the Refine and Advantages of Plastic Extrusion
In the vast world of manufacturing, plastic extrusion becomes a extremely efficient and crucial procedure. Translating raw plastic right into constant accounts, it satisfies a plethora of markets with its impressive adaptability. This guide aims to elucidate the complex actions included in this technique, the kinds of plastic appropriate for extrusion, and the game-changing benefits it offers the sector. The ensuing discussion guarantees to unravel the real-world influences of this transformative process.
Comprehending the Basics of Plastic Extrusion
While it may show up complex in the beginning glance, the process of plastic extrusion is fundamentally simple - plastic extrusion. It is a high-volume production method in which raw plastic is thawed and formed into a continuous account. The process starts with the feeding of plastic material, in the type of granules, powders, or pellets, into a warmed barrel. The plastic is then melted using a combination of heat and shear, used by a rotating screw. When the molten plastic gets to completion of the barrel, it is forced with a little opening called a die, forming it right into a wanted type. The designed plastic is after that cooled down, solidified, and reduced into desired lengths, completing the process.
The Technical Refine of Plastic Extrusion Explained
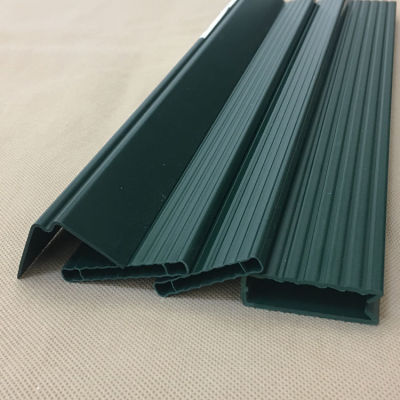
Kinds Of Plastic Suitable for Extrusion
The selection of the ideal kind of plastic is a crucial facet of the extrusion procedure. Different plastics provide special residential properties, making them extra matched to particular applications. Polyethylene, for instance, is typically utilized because of its low expense and simple formability. It uses outstanding resistance to chemicals and moisture, making it perfect for items like tubes and containers. Likewise, polypropylene is another prominent option as a result of its high melting point and resistance to fatigue. For more durable applications, polystyrene and PVC (polyvinyl chloride) are typically chosen for their strength and longevity. Although these prevail options, the selection eventually depends on the particular requirements of the product being generated. Recognizing these plastic types can dramatically boost the extrusion process.
Contrasting Plastic Extrusion to Other Plastic Forming Approaches
Recognizing why not try these out the kinds of plastic appropriate for extrusion leads the means for a broader conversation on just how plastic extrusion stacks up versus various other plastic developing approaches. Plastic extrusion is unequaled when it comes to producing constant profiles, such review as gaskets, pipelines, and seals. It additionally permits for a regular cross-section along the size of the item.
Trick Advantages of Plastic Extrusion in Manufacturing
In the realm of production, plastic extrusion offers several substantial advantages. One notable advantage is the cost-effectiveness of the process, which makes it a financially attractive manufacturing approach. Additionally, this strategy provides superior item versatility and improved manufacturing rate, consequently raising general production effectiveness.
Affordable Production Approach
Plastic extrusion jumps to the forefront as an economical production technique in manufacturing. Additionally, plastic extrusion calls for much less power than traditional manufacturing approaches, adding to reduced functional expenses. Overall, the financial advantages make plastic extrusion a very appealing choice in the manufacturing industry.
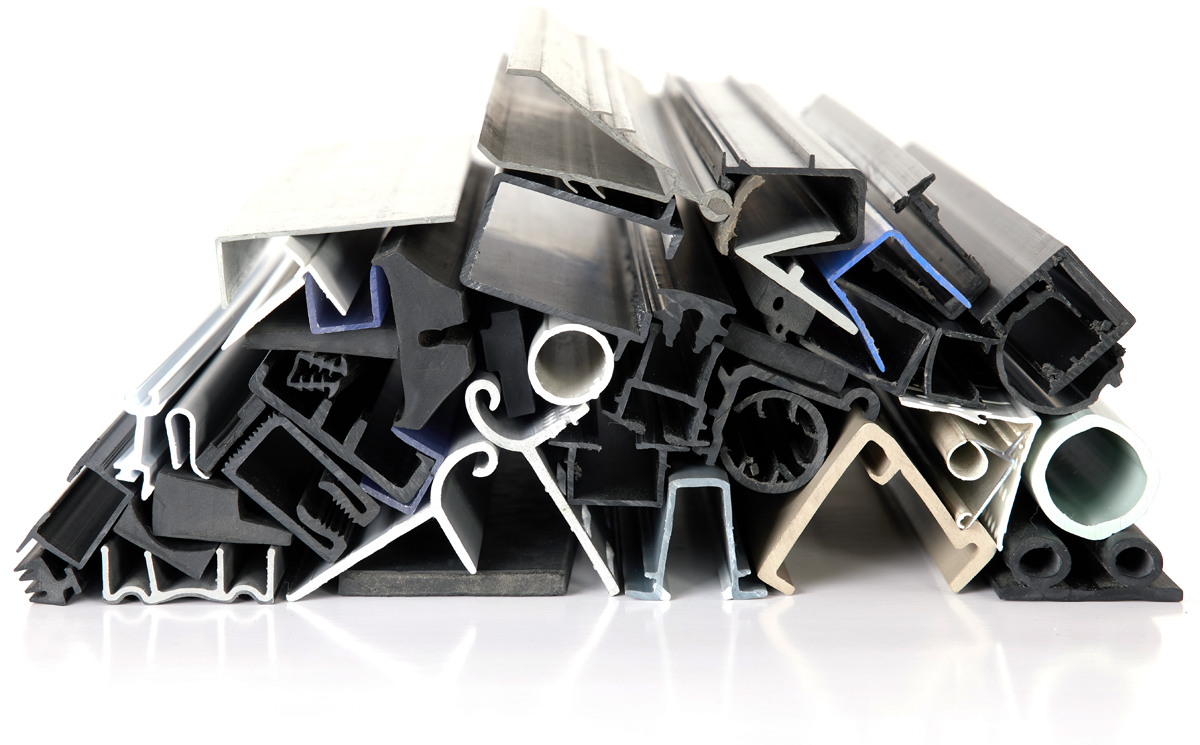
Superior Item Adaptability
Past the cost-effectiveness of plastic extrusion, an additional considerable benefit in manufacturing lies in its superior item flexibility. This makes plastic extrusion an excellent service for markets that call for customized plastic elements, such as vehicle, construction, and packaging. In significance, plastic extrusion's product adaptability fosters innovation while boosting operational effectiveness.
Enhanced Manufacturing Speed
A significant advantage of plastic extrusion depends on its enhanced production speed. This manufacturing process enables high-volume manufacturing in a reasonably short time span. It can creating long, constant plastic profiles, which substantially minimizes the manufacturing time. This high-speed manufacturing is especially useful in markets where big quantities of plastic parts are needed within limited deadlines. Few other manufacturing processes can match the speed of plastic extrusion. Furthermore, the capability to keep regular high-speed manufacturing without giving up item top quality sets plastic extrusion aside from try here various other techniques. The boosted production speed, for that reason, not just allows manufacturers to satisfy high-demand orders but additionally adds to enhanced performance and cost-effectiveness. This helpful feature of plastic extrusion has actually made it a preferred option in many sectors.
Real-world Applications and Influences of Plastic Extrusion
In the realm of manufacturing, the method of plastic extrusion holds profound relevance. The financial benefit of plastic extrusion, primarily its affordable and high-volume output, has actually changed manufacturing. The market is constantly making every effort for developments in recyclable and naturally degradable materials, suggesting a future where the advantages of plastic extrusion can be preserved without jeopardizing ecological sustainability.
Verdict
Finally, plastic extrusion is a extremely reliable and reliable technique of changing resources right into diverse products. It provides various benefits over various other plastic forming techniques, including cost-effectiveness, high output, marginal waste, and style adaptability. Its influence is exceptionally felt in numerous sectors such as building, automobile, and consumer products, making it a crucial process in today's production landscape.
Delving much deeper into the technical procedure of plastic extrusion, it begins with the selection of the proper plastic material. When cooled, the plastic is cut into the called for lengths or wound onto reels if the product is a plastic film or sheet - plastic extrusion. Contrasting Plastic Extrusion to Other Plastic Forming Techniques
Understanding the kinds of plastic appropriate for extrusion paves the means for a wider discussion on how plastic extrusion piles up against other plastic forming approaches. Couple of other production processes can match the speed of plastic extrusion.